Silicon PTC Thermistor Temperature Sensor, Axial Leaded Glass Sealed DO35 Package, Resistance @25C 1000Ω+/-1%, Operating Temperature -55C– +175C, Cross to NXP KTY83-110 Silistor.
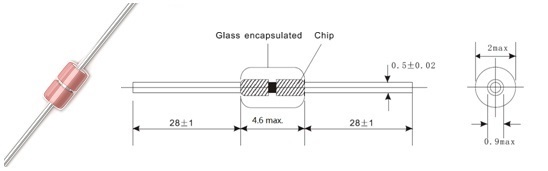
Unit: mm
- Silicon chip hermetically sealed in DO35 glass shell.
- Tinned Dumet wire
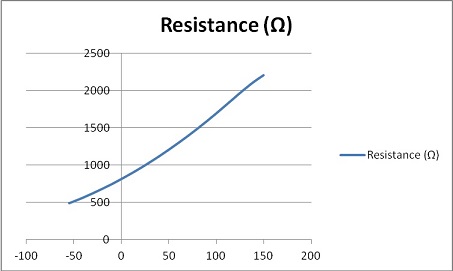
Silicon Temp Sensor 1K RT Resistance vs. Temperature Characteristics Temperature (Centigrade C)
- High accuracy and reliability
- Long-term stability
- Positive temperature coefficient;
fail-safe behavior - Virtually linear characteristics
- Motion control temperature sensor, temperature sensing and controls in drives and motors, spindles, inverters and control systems, etc.
- Industrial automation control equipment.
- Precision circuit and crystal oscillator temperature compensation.
- Temperature compensation of silicon semiconducting devices.
- Temperature compensation of instrumentation amplifier.
- A/D converter temperature compensation.
- Micro motor timing control.
- Automobile temperature detection and control.
- Medical equipment temperature detection and control.
- Linear PTC thermistors applications also include transmission, engine oil and coolant, heating system, overheating protection, amplifiers, power supplies, transducers, telemetry, computers, magnetic amplifiers, thermometry, meteorology, temperature regulation and over-temperature protection.
Resistance at 25C: 990–1010Ω
Dissipation Factor:1.5mW/C min. in still air
Thermal Time Constant: 21 seconds max. in still air
Insulation Resistance: 100MΩ (DC=100V)
Maximum operating current: 8mA max.
Rated operating current 2mA
Rated Power: 50mW max.
Temperature measurement range: -55C~+175C
Storage time 2 Years (Room temperature, relative humidity <60%)
Isen(cont) = 1 mA.
Ambient Temperature | Temperature coefficient (%/K) |
Resistance (Ohm) |
|
---|---|---|---|
(°C) | (°F) | ||
-55 | -67 | 0.98 | 487 |
-50 | -58 | 0.94 | 512 |
-40 | -40 | 0.92 | 562 |
-30 | -22 | 0.94 | 617 |
-20 | -4 | 0.91 | 678 |
-10 | 14 | 0.89 | 743 |
0 | 32 | 0.86 | 811 |
10 | 50 | 0.82 | 884 |
20 | 68 | 0.80 | 951 |
25 | 77 | 0.78 | 1000 |
30 | 86 | 0.78 | 1040 |
40 | 104 | 0.75 | 1125 |
50 | 122 | 0.73 | 1213 |
60 | 140 | 0.71 | 1304 |
70 | 158 | 0.69 | 1400 |
80 | 176 | 0.68 | 1500 |
90 | 194 | 0.65 | 1605 |
100 | 212 | 0.62 | 1713 |
110 | 230 | 0.60 | 1821 |
120 | 248 | 0.57 | 1933 |
130 | 266 | 0.57 | 2047 |
140 | 284 | 0.55 | 2168 |
150 | 302 | 0.54 | 2282 |
160 | 320 | 0.52 | 2384 |
170 | 338 | 0.51 | 2448 |
175 | 347 | 0.51 | 2512 |
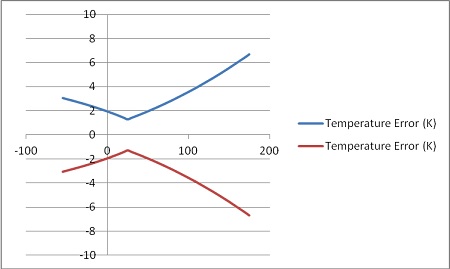
Minimum lead wire length tailored to shall be ≥8mm.
In lead wire bending, bending point shall be more than 2mm away from glass body part.
Mounting and Handling Recommendations
Excessive forces applied to a sensor may cause serious damage. To avoid this, the following recommendations should be adhered to:
- No perpendicular forces must be applied to the body
- During bending, the leads must be supported
- Bending close to the body must be done very carefully
- Axial forces to the body can influence the accuracy of the sensor and should be avoided
- These sensors can be mounted on a minimum pitch of >5 mm
Soldering and Welding
- Avoid any force on the body or leads during, or just after, soldering.
- Do not correct the position of an already soldered sensor by pushing, pulling or twisting the body.
- Prevent fast cooling after soldering.
- For hand soldering, where mounting is not on a printed-circuit board, the soldering temperature should be <300C the soldering time <3 s and the distance between body and soldering point >1.5 mm.
- For hand soldering, dip, wave or other bath soldering, mounted on a printed-circuit board, the
- soldering temperature should be <300C, the soldering time <5 s and the distance between body and soldering point >1.5 mm.
- The distance between the body and the welding point should be >0.5 mm. Care should be taken to ensure that welding current never passes through the sensor.